S6, E2: The Wild & Cozy World of Home Insulation Packages
When building a high-performance home, it's what is on the inside that counts the most. In this episode of The Art of Custom, we take a deep dive into one of the most critical aspects of energy-efficient building - insulation.
Building an insulation package that makes your home more comfortable, efficient, and healthier to live in begins with making informed decisions about what insulation options are available on the market today and what works best for your project.
We brought in Mike Pruitt from Goley Insulation to explore the different types of insulation products. From the pros and cons to building the right mix of products to maximize your home's performance, we explore how to make your home as efficient as it is beautiful.
You can read the transcript below, or...
Episode Tool Box:
See BIBs insulation installation in one of our custom home projects
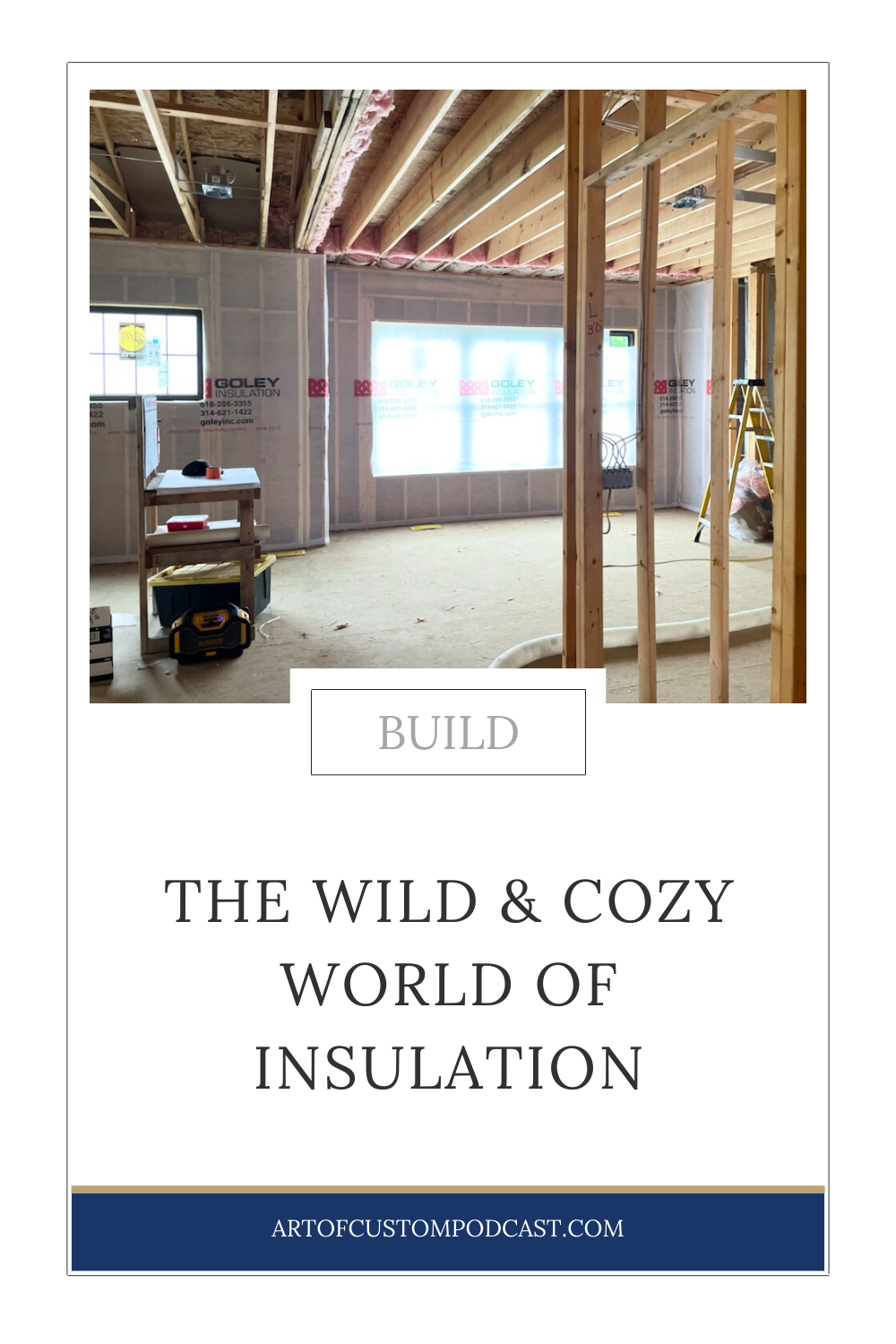
HIGH-PERFORMANCE INSULATION PODCAST TRANSCRIPT
MELODY: [00:00:04] When we say installation package, you really need to think about all of the different types and where they need to be used.
MIKE: Yes, specific materials do have specific qualities and you want to put them according to the style of the house that you're building.
INTRO: [00:00:21] Welcome to The Art of Custom from Hibbs Homes. In this episode, we are talking about insulation. Mike Pruitt with Goley Insulation joins us as we discuss the different options to keep your utility costs down while making your home safe and comfortable. Enjoy.
KIM: [00:00:39] Now, I know what you're thinking. Insulation really? That sounds about as exciting as watching paint dry.
While soaring utility bills and playing ‘guess how comfortable it is upstairs,’ may get your heart pumping, our mission is to help you make the best decisions when building your custom home. And if the adrenaline of utility bills is your thing, we're not here to judge.
So hold onto your hard hats listeners, because we're going to explore the wild and cozy world of insulation.
KIM: Melody, you've got a big smile on your face over there.
MELODY: This is actually an interesting topic to me because it's one that I cannot answer a ton of questions about
KIM: I know that I can and I know our guest can.
MELODY: In today's episode, we're going to talk about all the different choices you can make when choosing insulation for your home. There are the cool kids like fiberglass and cellulose spray foam, we use those everywhere, but we're going to talk about some of the underdogs like mineral wool and reflective insulation. Our listeners are going to come away armed with so much information it's going to be sure to thrill at their next dinner party.
KIM: Well and we've talked about this before, that thermal envelope. And to help define what that thermal envelope is, picture your house and picture this really large blanket that gets set on top of your house, anything that blanket touches is the thermal envelope. So it's kind of touching the exterior of the home, the windows, the doors, the siding, the brick, the stone. But inside that is the insulation. And the insulation, in my mind as a high-performance builder, the insulation is the most important component of this build because it's going to determine how that house performs and what you need to do with the rest of the house, like your HVAC systems, your windows, your fresh air and all that.
So, insulation is a critical subject that we're going to be talking about and when you put out our topics to discuss and season six, when I saw insulation, I was thrilled.
MELODY: AWell, good. And I am really glad to hear that, and we're going to have Mike Pruitt from Goley Insulation come on and talk about insulation with us.
KIM: [00:02:55] Mike, thank you so much for joining us. It's nice to have you with us for the podcast. We've been working together now for well over a decade, and one of the reasons that we enjoy working with you is your kind of a student of the science of insulation. Talk a little bit about your history with insulation, and how you got into the industry and why it's so important for you to stay on top of the changes in the industry.
MIKE: I got into the industry about 35 years ago. I was an installer for the first 10 years, then I moved up into the sales position and have done residential and commercial jobs. The building sciences are getting more and more important, or being more and more recognized, and what needs to be done in houses to make a well performing house.
KIM: So, let's just start there. When you're talking about a well, performing house. Obviously, insulation is the key factor, when you Here, the term R-value help our listeners understand R-value, what it means and how it's used in the industry.
MIKE: The R-value, the definition is the resistance to heat flow. The higher the R-value is the better the performance is going to be because it's going to be allowing you to control the heat that's migrating through a material.
The other portion that's important is going to be the air sealing of your house. And between those two, they're going to affect how comfortable you are and the performance of your house.
KIM: And something else we hear in the industry is grade 1 insulation. So, tell us a little bit what that means and how it's used in your industry.
MIKE: Yeah, Grade 1 Insulation is making sure that the installation of the insulation is put in so the bat is behind the wires behind the outlet boxes, making sure that it's a pretty full cavity fill. If you smash the insulation in there you do not get that R-value so you don't get the performance that you would, if the bad Is not properly installed.
KIM: Okay. Are there any other terms that we should kind of set the table with, for this discussion? We talked about R-value, we talked about Grade 1 Installation, is there anything else that would be helpful to kind of set the table? So when we take the conversation further, our listeners will understand. Melody has one
MELODY: Thermal bridging.
KIM: Thermal bridging, what is thermal bridging?
MIKE: Thermal bridging is where your stud in the wall cavity is your biggest thermal bridge. It has a lower R-value than the rest of the cavity that allows the temperature change to reflect from the inside to the outside more often and will decrease the total R-value of the wall.
MELODY: We talk a lot about thermal envelope, that's why I don't think we had to define it but can you explain to me how it functions as part of the thermal envelope.
MIKE: The insulation is going to give you the R-value in the thermal envelope which is the shell of the building. You want to make sure that you have the complete shell all contacted and wrapped like a big surface area there. You want to do the perimeter of that surface area to keep your indoor air that is conditioned separated from the outdoor air, which is not conditioned. The more often those two change places, the more it's going to cost you and the less comfortable you'll be in your house.
KIM: Mike, in episode number one of season six we were talking a lot about the differences between production, semi-custom, and custom homes. And I think this is probably a good time to talk about some of the important factors like insulation. In a production build, the builder basically has specs and that's what you're going to get in your house. In a semi custom build, I think you have a little bit more flexibility. But in a custom home, if most custom builders are like Hibbs Homes, they are going to help educate you on your insulation options, best practices, what they would recommend, and you're going to have a lot more overall options as far as your installation package.
MIKE: Oh definitely it is because the production builder is trying to turn out houses. People don't generally know what they get in their walls, so they don't have any choices on it. They get the normal fiberglass batts pushed into the wall, a lot of times it's not stuffed behind the wires, or outlet boxes. So you have those traces and pathways behind the wires where the air flows right up to the outlet boxes. And that's where you get the drafty outlet boxes for one and the higher utility bills.
With a custom home, though, you get to specialize in each area like the rim joist on a house, which is below the subfloor and above the foundation. That area is where everything meets. That is an area where you really would like to use a foam insulation sprayed in and applied to air seal it. Which in a subdivision home, you're not going to get that choice and it’s all the way throughout the house.
The blown-in-blanket system is an excellent system for walls. As opposed to just regular batts, that is where we put up a mesh, a little fiberglass in behind the mesh and completely fill the cavity. That way you don't have the human error, you have a hundred percent coverage in the cavity behind the wires, the boxes, everything in the corners, behind the wall T's and you just get a perfect cavity fill on that.
Plus with your attic insulation you really want to air seal and tighten. Any leaks going up to your attic space which you're not really going to get in a subdivision built house,
KIM: Right and we're going to talk more specifically about all those options and I'm really glad you brought them up. The one thing before we launched in, I want to mention that the codes are changing and the codes are making it more standard for even the production builders to take a look at their insulation package and improve the insulation package iIn some areas.
MIKE: We're seeing a lot more inspections on homes and stuff. That is going to increase the subdivision builder, but just to the point of what they have to do. Rather than custom home builders who are going to actually pay attention to all the details, make sure they get better than code houses
KIM: And also, since we have listeners from across the country, I want to make sure that people understand that we have different zones throughout the United States and those buildings zones, your codes and requirements for your installation package can change, your R-values and things like that. And the way insulation is used quite frankly. So always get on board and make sure that you're working with a good qualified insulation contractor.
So let's launch in and talk about some of the options that you mentioned earlier. Fiberglass batts that's the tried-and-true. I think everybody knows about batts, correct?
MIKE: Yes, and fiberglass batts do a good job in giving, as long as they're installed properly -a grade one install, then fiberglass batts do give you a good R-value in the side cavities to help you protect your walls from the outside.
MELODY: Are there any cons to using fiberglass insulation over another type?
MIKE: Mainly, the fiberglass batt is like the entry level. It does a good job at a very good cost. It's usually just the cost of the fiberglass batts is where you'd want to use it more. Like in sound walls, usually in fiberglass batt is going to be the thickness of the stud cavity, or three and a half inches thick, and going to stop about as much as if you would use a blown-in-blanket system or something different, and do it at a much more reasonable cost.
KIM: Since we're talking about fiberglass, and you mentioned it a minute ago, the BIBs, the blown-in-blanket system, that's what we use in them in many of our homes because it's just a much better process if you will and product. Take us through a little bit more in detail what that blown-in-blanket, the BIBs system, is all about.
MIKE: The blow-in-blanket system is going to give you a great R-value reasonably priced. It is more than the batts, but due to the full cavity fill that you get, it's 100% filled - every available spot gets filled with insulation. It's a higher density than batt insulation, and it gives you a higher R-value than batt insulation or any other product other than the two pound foam. Two pound foam will probably be getting to a little bit later, but there they are the most expensive way to do it.
MELODY: So my question is sound absorption. Is there any difference between the different types of insulation? In terms of making your home quiet?
MIKE: The important factor of sound insulation is the thickness of the material not the density of the material. If you go to, this will be on the commercial end, they have what they do testing for sound transmission classifications. And if you put say a high-density rock wool or thermal fiber type product into a wall cavity, or if you put a lower density fiberglass batt into the wall cavity, they will come up about right at the same sound transmission classification between each of the two products. It just matters the thickness. The key to deadening sound more is to go with a thicker material, not a higher density.
KIM: So we talked about it, we're big fans of the BIBs system because of its performance. It does lead to a much quieter home, and also because we feel like it's fairly priced it's a really good value for the benefits you get. But you mentioned a minute ago, foam and said we were going to circle back around to it. So I think this is a perfect time to do just that. We actually use a combination of foam and the BIBs system, at your recommendation to start with. And we've tried it, it works exceptionally well. Tell us about the use of foam. Let's start there. In insulation, why do you use foam in your installation packages?
MIKE: Okay, the most important quality that the foam has is that it does an excellent job in air sealing. Your two things which you’re looking at, I think I mentioned earlier, were R-value and air sealing the house. You want to build your house tight so that you're in control of how much air leakage you get in and out of the house. Foam’s big asset is that it does a great job sealing off a house, it does it but it does have a cost to it.
There are certain areas of a house where foam is the best product to use all the way through. Your rim joist where everything meets, that's where you are going to have a large part of your air leakage. That is an excellent place to put foam. If you have a room over a garage, the floor of that room is another very important spot to use a foam insulation. It will adhere to the bottom of the floor in that application and seal so no air can get over the top of it.
KIM: Some people are actually using foam all the way through the house. Talk about the benefits of that, and I think the drawback is going to be the price, correct?
MIKE: Yeah. The only drawback is the price. If you want to spend the money, then spray foaming the outside walls is a great idea. But, it is very costly to do that. When you're building a wall cavity, you as a builder, pay attention to the details to air seal that cavity off anyways and make it tight. So, when you're paying attention to the construction as you're building it, you can get the same results in a house without spending the extra money on foam.
MELODY: So we've talked a lot about thermal bridging, but there's a moisture component to insulation as well. What material would you recommend for the best moisture resistance?
MIKE: The foam is a great moisture resistant material. Whenever you're looking at the moisture control on a house, you want to watch for two things. We used to have a philosophy of the house only dry to the outside and we'd use poly-vapor barriers and stuff. We’re away from poly-vapor barriers in the St. Louis climate area because we are better off not having as good of a vapor barrier because when you put the vapor barrier up you can trap moisture, as well. Without using the plastic anymore, we're allowing for drying to the inside as well as to the outside. So if you get moisture buildup in your cavity from condensation, temperature changes, you're allowing that cavity to dry out quicker and as long as that wall cavity and any moisture in it gets dried out fast enough, you don't have those extra issues with mold.
MELODY: When you're talking about a vapor barrier. as someone who is coming at it from, not an expert installation perspective. I heard an interesting story, and I wonder if it's the same thing. There was a collapse of a brick building because the bricks were painted and it trapped the moisture between the brick and the paint, and so it actually ended up with the bricks crumbling with the paint, in that example, be like the vapor barrier?
MIKE: Some paints can be the vapor barrier depending upon the paint. There are specialty paints that are made to be a vapor barrier. It would depend upon the entire set up on how that was built to evaluate it. If it's causing the brick to crumble, then it is probably the vapor barrier and it's holding the moisture into the brick.
KIM: So again, I want to be clear what you're talking about, in the St. Louis area we are not using a vapor barrier because we want the moisture to be able to go in both directions because we heat half of the year and cool half of the year. I will say, we've actually used in some of our homes vapor barriers that allow that moisture to transfer in both directions. I know that it is out there available now. But I guess my point being, in different parts of the country vapor barriers are going to be used and they're going to be used and they’re differently because some, like up north where they're heating more than they're cooling, or down south where they're cooling more than their heating, different rules apply for the installation of insulation. Correct, Mike?
MIKE: Exactly. We are a mixed climate zone and that's why we do things. We're going to apply the vapor barrier, according to our mixed climate zone.
KIM: But I think that the overall conversation we're having, between Grade 1 batt, or the BIBs system, or the foam. The actual installation or performance of that will not change, it's just the density that we're using or the vapor barriers might change depending upon the part of the country or the R-value.
Now, before we move on from foam, there is another option. We talked about how expensive foam can be, but another option that we've tried, and I know other builders have, it’s called either a ‘Flash and Batt’ or a ‘Flash and BIBs System.’ Where you do kind of a skim coat of the foam on the inside of the studs and the sheathing, which is going to air seal the house. And then you come in and you either put a blanket or BIBs on top of that. So it does help mitigate some of the cost, but it also gives you a really good performing installation package, right?
MIKE: Oh yeah. And that's also an option up in the attic space too. You can skim coat the attic space and then backfill it with blown-in, I would recommend a fiberglass, it's optional on both the walls and the ceiling. In your attic, you have a lot of potential air leaks where your drywall meets your top plate. If you go into your attic space before the insulation, you can see every top of every wall going in there and on each side there's a little gap. And that's an important spot. Houses have different pressures from inside and outside, and so you get a sucking motion going through there and it will suck a lot of the inside air out into the attic space so you lose a lot of your conditioned air. The skim coat in the attic is one way to do it. The other thing that we do is, with the drywall gaps we go by in a lot of your houses and we will seal the top plate to seal that gap up at a much lower cost.
KIM: And basically, when you're talking about the gasket, it's almost like it's an adhesive and you put it along the top plate, right underneath your trusses. So whenever you apply the drywall and it gets screwed into place, it's going to provide that sealing that we've been talking about.
Now, one other thing that we as a custom builder do to help the installation package is, we raise the heel of our roof trusses. And by that we simply mean we're going to try to give you a little bit more room over those outer exterior walls to extend your insulation out over that wall. So talk about that process of raising the heels of the trusses and the importance of getting more insulation out over that exterior wall?
MIKE: Yes, that area there, if you can't get the full area over the outside walls, they actually in the energy codes require a higher R-value in the entire attic to make up for that loss. It is a big issue iIf you can't get a good R-value out of your outside walls, because in houses in the past you'd only have like three or four inches over the outside edge of your wall. There are formulas to calculate how much loss you get from that, a total area weighted R-value, and it really degrades your entire attic insulation to where you have to have quite a bit to make up for that.
KIM: And by raising the heels of the trusses, I simply mean adding 12, maybe 18 inches of space in between the exterior wall that allows extra insulation to get out over that top plate. So just make sure, if you're designing a home, you tell the architect a little bit about the benefits of raising the heels of your trusses in your particular environment and see if that makes sense.
MELODY: So there's another fancy term that we didn't talk about up front because it has more to do with framing: it's California Corners and that helps with insulation, as well. So can you guys explain what a California Corner is?
MIKE: Yeah, California Corner is framing so that we can so that the insulator can get insulation into the corners of the building. In other methods you don't have any insulation in the corner of buildings; it's all wood. We talked about thermal bridging on the wood, so you don't you don't get the R-Value in the corners. And also like where your interior walls come off your outside walls building those in what they call ladder style framing, that way we can get the insulation behind it. Those framing methods are designed so that the insulator can get those corners insulated. That's where the BIBs does a great job really filling behind those areas you can't see.
KIM: The other thing that's critical in an installation package is to make sure it's a very, I don't care what part of the country you live in, a caulk and seal package. Talk about what happens during the caulk and seal and why that is something that every homeowner should be asking for when their home is being built.
MIKE: Yes, around the base plates of all your exterior walls is where a lot of your materials are all meeting together. So you can get a nice sized air gap coming in below the bottom of the walls. A little bit of caulk goes a long way in air sealing those spaces, the corners are areas where foaming to the attic plates, that drywall gasket going up to the attic space, all that stuff reduces and puts the homeowner in control of the air that's coming and going from their house.
KIM: And I will also say, make sure that your insulator uses low expansive foam around all your windows and your doors and if you have any exterior outlets and things like that because the typical fiberglass that's pushed into place does not work nearly as well.
Since we're talking about using foam and you mentioned the term earlier about building a very tight home. There's a phrase in our industry: “build it tight but ventilate it right.” So we're going to build a very tight home, most of our homes are tested, so we know exactly how much air is coming and how much is going. But it's very important if you're going to build a tight home, make sure your builder, your architect, your HVAC contractor, and your insulation contractor work together to determine the amount of fresh air that needs to be introduced into the house. So you have that well-balanced.
MIKE: Yes, yes, exactly. There's a few different methods that you can use in order to get in that fresh air. But you want to keep it under your control so that you can decide. You want to keep a good healthy house by bringing in the proper amount of air. And doing it mechanically, you have control over how much air you are going to bring in and, if situations change, you can change the amount of air you’re bringing in. It's just totally in the homeowners control at this point, which is great. They never used to do that. Houses we build today are pretty tight.
MELODY: Another one of the cool kid insulation types is cellulose, and we haven't really touched on that. Can you explain cellulose and what exactly it is?
MIKE: It's got some good properties on it. I don't like the fact that it’s a paper based product because it will absorb moisture. I like fiberglass because it is a rock melted to glass and spun into fibers. So you have the permanence of that material.
The cellulose is ground-up newspaper and it will absorb moisture later on. So, as we get this condensation or anything taking place in your wall, especially here in St. Louis area with our different climates, we're going to at some point have a little bit of moisture in the wall. I don't want it absorbed into the insulation material. Whereas glass, it will not absorb any moisture into it. That being said, in an attic space there are some advantages. It is a heavier material and it does pack tighter. I prefer fiberglass for the base material products all the way through the house.
KIM: Melody, that was a good question because quite frankly cellulose, especially a decade ago maybe even a little bit more, was extremely popular and I know there's still a lot of people who install it today. So, I want to be clear, we're not saying do not consider it. Maybe in certain parts of the country, maybe your builder, maybe your insulation contractor, has really good results with it. This is just Mike's preference and he prefers - and we don't use cellulose either. But I always encourage people to look into all sorts of options and talk with their professionals about what those options are.
MELODY: So when would that be the right choice? It is you're saying it's very zone dependent, then?
KIM: I'm not, I don't know enough about it. I know in this particular climate we don't use a lot of it simply because of the moisture component that Mike talked about. But then he also mentioned that if you use it up in the attic, there might be a proper option for it. I guess my point I'm trying to make is to talk with your independent insulator, your HVAC contractor, your builder, and work with them to make a choice that is best for you.
What other options are there out there that our listeners should be aware of?
MIKE: We looked into, a long time ago, I remember having a meeting discussing plastic installations on the wall. It was a plastic fiber blown in like the BIBs system. But we looked through it and determined it wasn't a good fit for our area. We had issues that we did like about it. The owner of Goley is pretty good at staying on top of the new products coming in to check into things to see if they're worth it. And worth it, will use them if they're not then we won't.
But the reflective materials, I'm not that fond of them. I just don't think they do as much as they promote. I’m not saying there's anything wrong with using them, but I don't really support them. It's not something I would exactly put in my own house.
MELODY: So if you're making a choice on what type of insulation, say, you're doing a renovation project and you have all of these options laid out in front of you. What is the first question you should ask yourself before making the choice?
MIKE: It depends on the area of the house which material is going to be applied. I think the best way to insulate the house is by using the appropriate material in each different area. Like the rim joist, that's the place to use the foam insulation. The upper walls, I would normally use the BIBs insulation. And then the attic insulation, just do a good job sealing your attic floor with a combination of the drywall gaskets and the foam sealing the wire holes. And then put a decent R-value over the top of your attic space. That's how I would do almost any house. Like we said, the room over the garage takes a little bit of special attention. It just depends upon the style of the house. There's different materials that work better in different areas.
MELODY: So really, it's a complete package. When we say insulation package, it's not just, this is the batts that go in your wall and your attic. You really need to think about all of the different types and where they need to be used.
MIKE: Yes, yes, it's specific materials do have specific qualities and you want to put them according to the style of the house that you're building. And by style of house, I just mean each area and what each house has. Houses are different and there's a little bit of difference in the way that you'd want to insulate even two different houses that Hibbs is building.
KIM: So just adding a couple of comments as a custom builder helping our listeners understand some of their options. I think that if you're building a custom home I would highly recommend spending a little bit of extra money to foam the band boards of your home. First floor or second floor or both. I'm finding that usually that's in the 2,000 to 2500, maybe 3000 to 3500 for larger homes, but that's such an important area to air seal and insulate.
BIBs is something else that we're very keen on. I’ve found that for most of the homes we’re building, that's an adder of 25 hundred, maybe 30, 35, 40,000 depending upon the size something to consider. But again, think about it this way, let's say you spend an extra five, six, seven thousand dollars on insulation. And let's say you spend another five or six or seven thousand dollars on your HVAC package and maybe a little bit more on windows.
If you put a total, Melody, of 20 or 25 into your home, the performance of the home, meaning your heating and cooling bills, is going to be so much more improved. The comfort of your home is going to be so much more improved. And the payback will be there too. A few years down the road, these will pay for themselves. So we're not talking about a big investment.
And speaking of not talking about a big investment, Mike, I think you'll agree with me on this. Sound proofing is such an inexpensive option when you're building your home to truly think about where you need it. Around powder rooms, maybe if you need to put it around a laundry room where there's a washer and dryer. You don't necessarily need it if there's a closet that buffers some of these rooms, but I highly recommend it if there's a first floor master suite, or primary suite, that is adjoining a great room with a television and fireplace - that big wall there. If you're finishing some of the lower basement consider putting some soundproofing insulation maybe in the flooring over the rec room. So strategically, think about soundproofing, Mike, and it's very inexpensive to install when you're building a home, right?
MIKE: Yes. And that's the one thing that a lot of people don't consider when they're building their house. They just don't think about advantages in putting some sound batts into the house to keep it quieter for later. If you're finishing a basement, off a lot of times, it's good to at least look into the cost of insulating the entire ceiling or most of the ceiling, or at least like, over the rec room. For the rest of the house, if you have bedrooms stacked on top of each other, you may want to consider doing the floor space in there as well for sound. Your insulation basically should be viewed as an investment in the quality of your house along with the other upgrades, like the windows and the HVAC. Those are investments that will supply a return. You have one chance to do the insulation and do it right the first time.
KIM: Well Mike, thanks for your time. The title of this particular episode was ‘Wild and Cozy World of Insulation,” and I think we've pretty well covered the subject. Thank you for your time. We greatly appreciate it and continue to do great work on the Hibbs Homes that you're insulating well.
MIKE: Well, thank you.
KIM: [00:30:18] Did you like how excited I got when talking to Mike?
MELODY: I did.
KIM: Now you understand why insulation is so important, right?
MELODY: I do and I think it's interesting that even the way that you build your home and the way you design your home is going to have a big impact on what type of insulation you're going to use.
KIM: I mean something as simple as when we talked about raised heels for your trusses, raising those heels so you can get more insulation out over your walls. Something like that is just not done in the production world. And as we talked about in episode one, love production builders, there's absolutely a need for them. They build good homes. But when you go into the custom world you can do so many more things. You have so many more options when it comes to the design. So many more options when it comes to what your insulating choices are. So that, again, shows you the true differences between the custom home building experience and the production home building experience.
MELODY: The quality, I think that speaks to the quality too. Sometimes it's really hard to define why you're spending a little bit more, but you are getting a higher quality because you're getting more performance value than you would with a home that's performing just like your neighbors.
KIM: And that performance value you're talking about, let's cut right to the chase, it's saving you money every single month and operating cost because your heating bills and your cooling bills are going to be lower because you did invest a little bit more upfront in your insulation package. My goodness, if there's one takeaway it's to spend the extra $5,000 dollars to insulate the home properly. Because I promise you, you're going to feel the difference in comfort and the payback period is going to be maybe five years, maybe three years. somewhere in that area. And then from the comfort standpoint and from a value standpoint, it is absolutely worth it to spend the little bit extra.
KIM: And if you have any other questions about installation, HVAC, all kinds of stuff that we're actually going to cover this season. You can always drop us a line at 314-266-9709. We might include your question in a future episode. Rate and review us on Apple Podcasts and subscribe.
KIM: You know, we talked about what a cool season six is going to be. One of the topics that we are going to be discussing are 3D printed homes. I'm hearing much, much more about that technology. I'll be honest though, I know very little about it. I know that ICON is one of the leaders in the industry. And I happen to know somebody within ICON and I've been trying to coordinate an interview with Spencer. So as we are taping this episode, our hope is that as we go on into episode three, this year, that Spencer with ICON is going to be our guest. We're going to be talking about that 3D technology so he's going to be on at some point this year. We believe it's going to be in the next episode. Just join us because I think it's a conversation that people will learn a lot from including me
MELODY: as the producer of the show. I have to say even if it's not the 3D episode next, I'm sure it's going to be thrilling.
KIM: Oh, absolutely nothing less right for our listeners, nothing less. Well, anyway, whatever we talk about, most likely 3D homes, we certainly hope you join us for the next episode of The Art of Custom
OUTRO: [00:33:31] For more information visit www.artofcustompodcast.com or find us on Facebook and Linkedin as The Art of Custom. Be sure to subscribe to get the latest episodes and please rate and review, The Art of Custom is produced by Hug Monster with original music by Adam Frick-Verdine. Thanks for listening.